Ultrasonic Welding is a process whereby high frequency vibrations are locally applied to components via a bespoke welding horn.
The process of ultrasonic welding is particularly useful when the design of the plastic component is too complex, or tooling too cost prohibitive to be moulded in one shot of an injection mould tool. Or indeed overmoulded. Where this is the case, often components can be designed to be joined together post moulding.
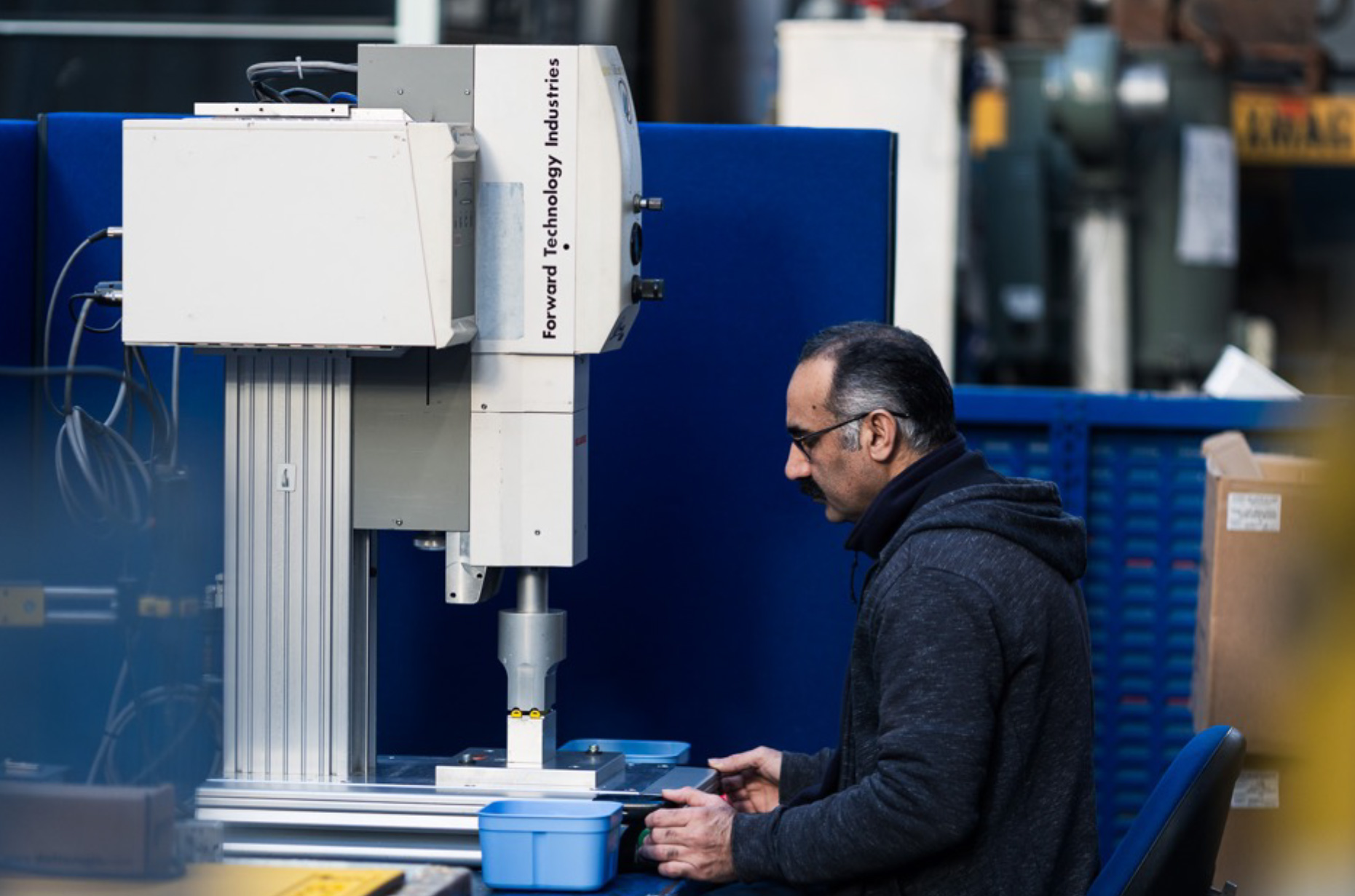
Despite being a secondary operation, it is a cost effective solution that is fully repeatable, whereas gluing cannot be easily monitored.
The benefits of ultrasonic welding is clear within the Medical device assembly, as it is does not require adhesives and does not create dust etc, it can be safely used without introduction contamination. Thus it is also a suitable method to be used within a cleanroom environment.
The introduction of ultrasonic welding was a customer driven investment, as with the Pad Printing. During a supply chain review, a long standing customer approached us to handle all three processes on their components – the first being the initial moulding. This removed multiple handling and shipping of product to two additional subcontractors.
Reducing costs not only within the administration of orders, the subcontract processes, but also the courier charges moving product between locations. Additional benefits being they could reduce stock holding of parts at all three stages to ensure a smooth supply.