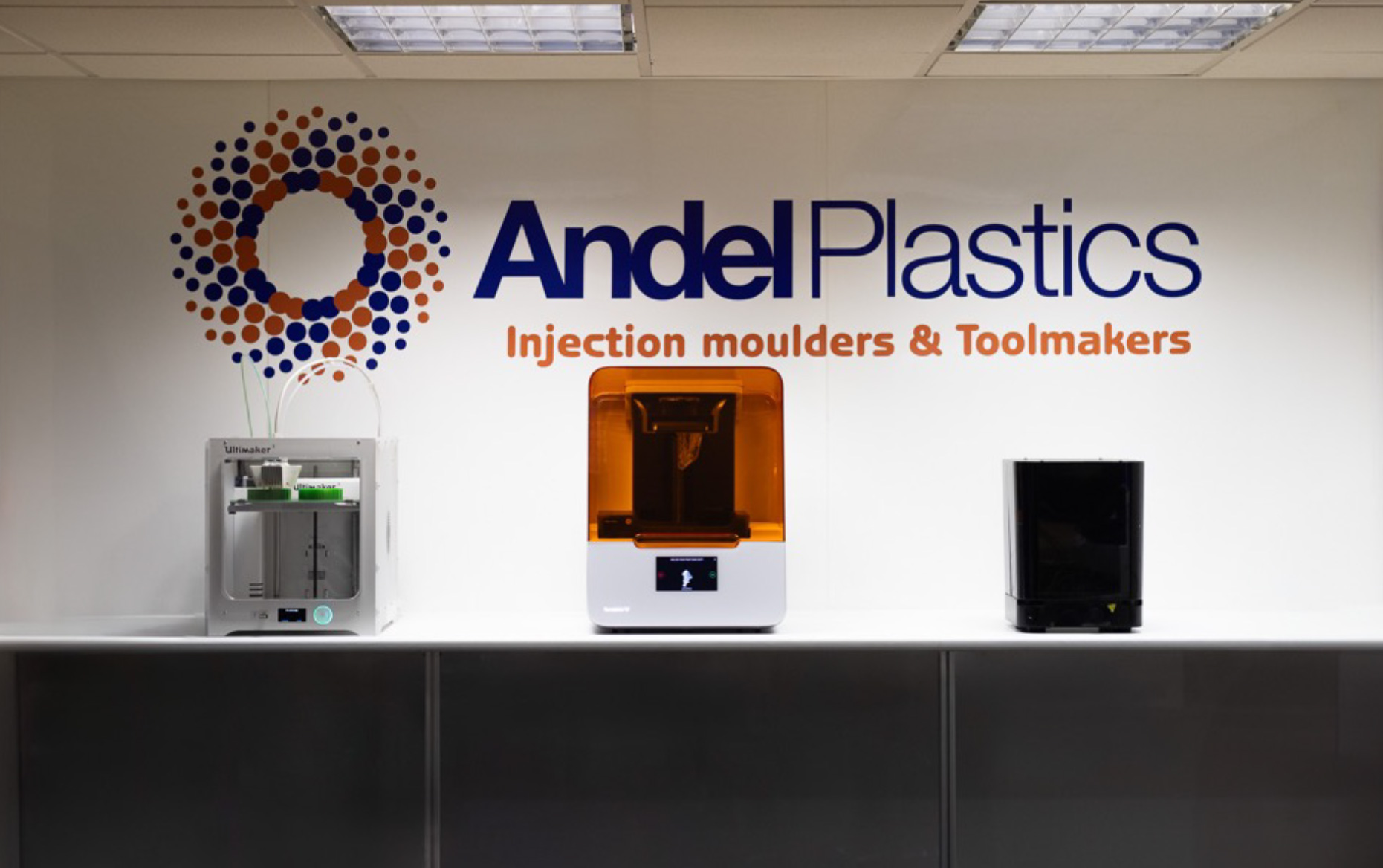
At Andel Plastics we have invested in researching and developing how Additive Manufacturing – 3D printing – can assist our customers.
3D printed parts have been available for many years and are often invaluable during the design and concept process. However, they are not truly representative of a part that has been injection moulded itself, which limits the testing possibilities.
Initially partnering with both Aston University and the Warwick Manufacturing Group. We developed several R&D projects, to test and evaluate the use of 3D printing to manufacture the prototype injection mould tool itself. During these projects we achieved much more than we were expecting both in the 3D printing of polymer tooling, but also metal 3D printing.
Having proven the technology, Andel purchased their own 3D printer with funding from the Made Smarter programme and are now offering this service to new and existing customers .*
This method has enabled customers needing prototypes for testing or market research to greatly reduce capital investment and lead times for moulded products, even when compared with aluminium tooling.
3D printed polymer tooling is not limited to a few prototype parts either. Andel has produced over 1000 shots on a small 4 cavity tool before seeing a degradation in the parts or tool. For the customer, calculations showed it was more cost effective to re-print a set of tooling for the small production runs when required, rather than manufacture production tooling.
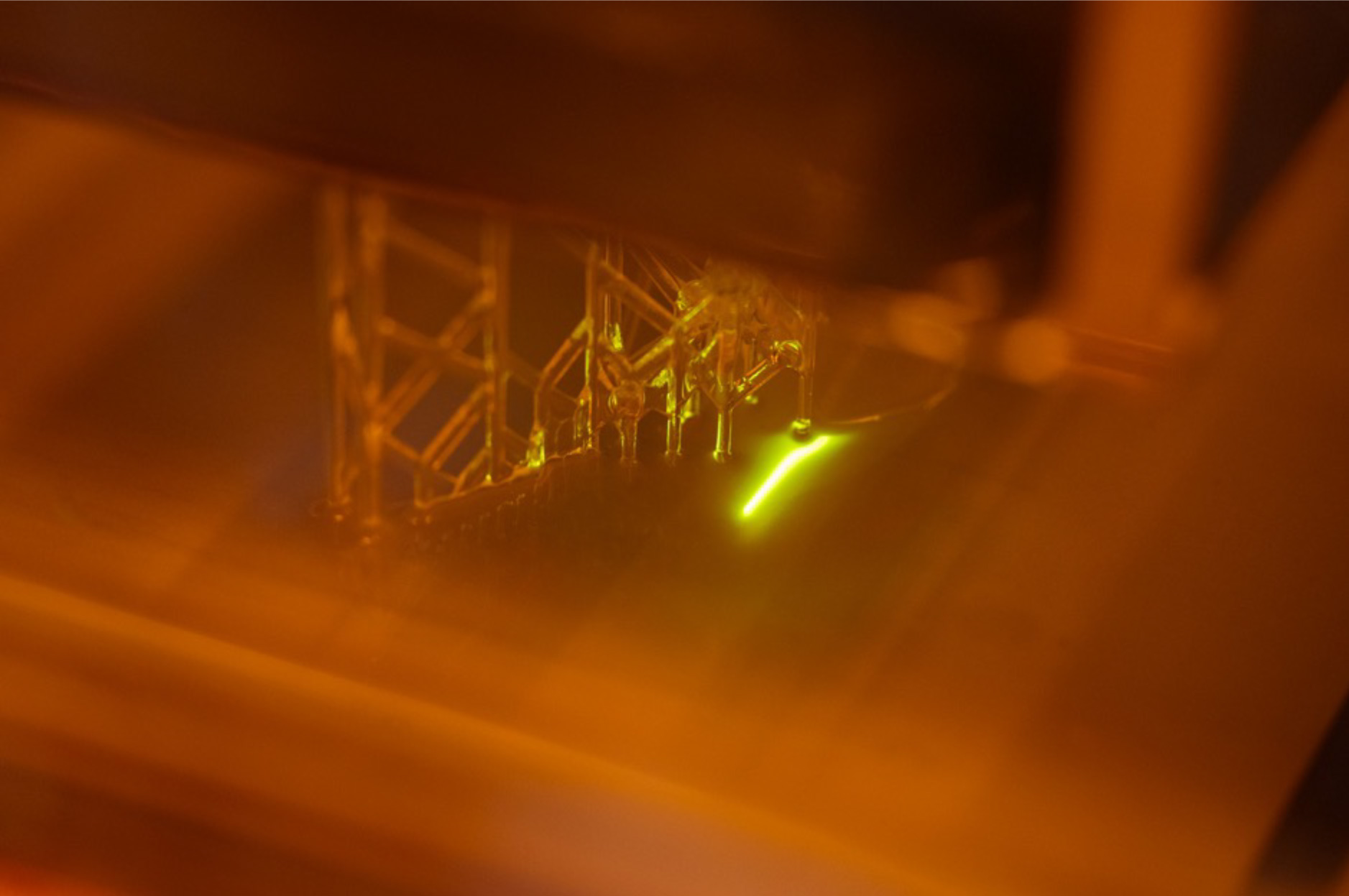
The cost effectiveness of the 3D printed tooling also gives the opportunity to test different iterations of a component at the same time. Without the restrictions of trials and tooling modifications that occur within the traditional injection mould tooling method.
Case Studies 3D Printing Tooling - Austin Healy Badge
Andel Plastics has been working with the automotive industry since it was established in 1975. However, our focus has not been limited to new model vehicles, in fact more often we provide parts to classic cars and aftermarket services.
Classic Jaguars, Morgans, Minis, Landrovers, we supply from newly made tools or with what you could describe as classic OEM tooling.
One of our customers had an original tool with a complex Badge pattern for the Austin Healy horn push. We were asked to make this an interchangeable insert tool to be able to bring back into production an old existing tool which produced the classic bonnet badge but was missing the emblem.
Anticipating an potential issue should the original insert be damaged during the process we sent the part to Central Scanning for a full scan and recreation into a CAD model.
Using our inhouse 3D printers we reprinted from this file to ensure it’s accuracy.
Having worked with both Warwick Manufacturing Group and Aston University on developing 3D printed tooling. We manufactured a 3D metal printed insert from the CAD data provided in the Scan.
Careful post printing treatment and machining gave us a successfully replicated insert that was then fitted into the tool. The tooling was then transferred to our mould shop where is manufactured perfectly the acrylic mouldings ready for metallising and decoration.
The picture shows the steps from original insert, 3D print plastic, 3D printed metal insert, moulding and finalised product.
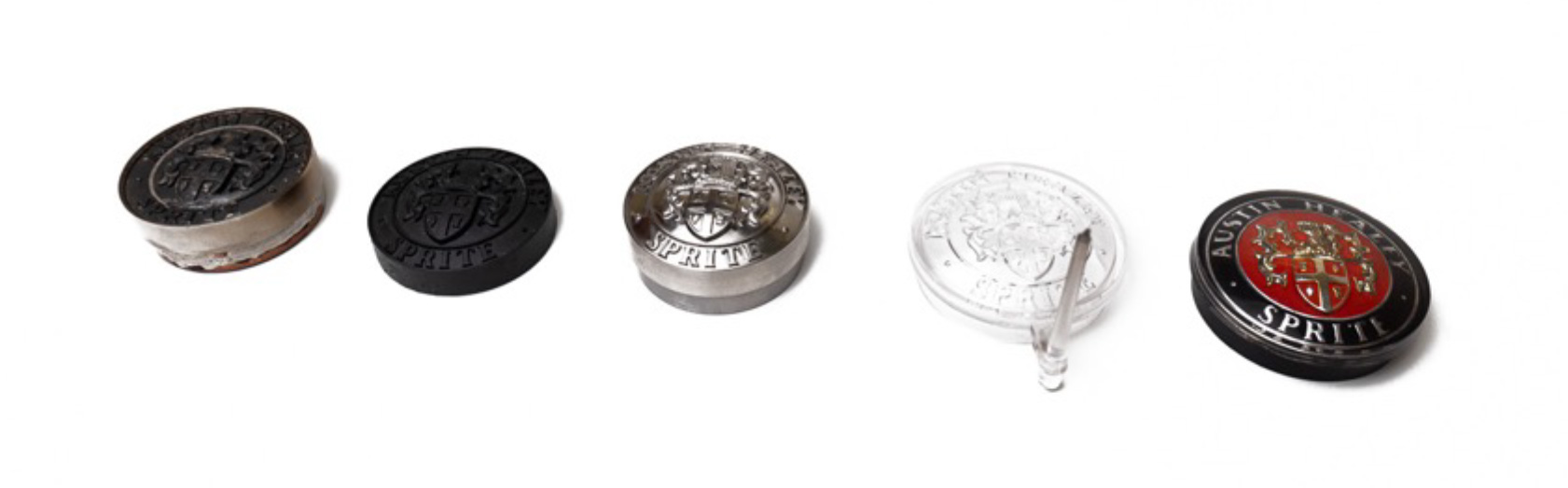
Testimonials
ANDEL Plastics offer expertise, understanding and innovative outcomes to a whole suite of areas we work in.
Being so much more than a me-too manufacturer, and having the ability to work in a collaborative manner enables us to grow the relationship long term and constantly plan for future areas of improvement.
Moflash has worked with Andel Plastics for over 26 years & in that time the quality & service has been second to none. Any successful commercial enterprise between two companies relies on the trust that both parties bring to that Relationship & we have always felt that Andel Plastics have gone out of their way to maintain it. I would highly recommend Them to any new customers who are looking for either injection moulding or tool making capabilities in the UK.
Great company to work with. Super helpful with refining designs and suggesting improvements and even creating new ideas when I was stuck, wouldn’t hesitate to recommend.