Within our state of the art Birmingham based factory, we offer injection moulding services ranging currently from 50 to 200 tonne.
We embrace automation collaboratively with our skilled workforce, reducing many of the repetitive processes. Including a 6 axis robot, we have been able to reduce bioburden on medical components, inspect them with a vision system and package them. This type of system maintains quality, cycle times and reduces the possibility of human error.
Our moulding facility with currently 20 machines, uses the Intouch Monitoring Cloud based system, for real time data collection, planning. Keeping traceability of all moulding production.
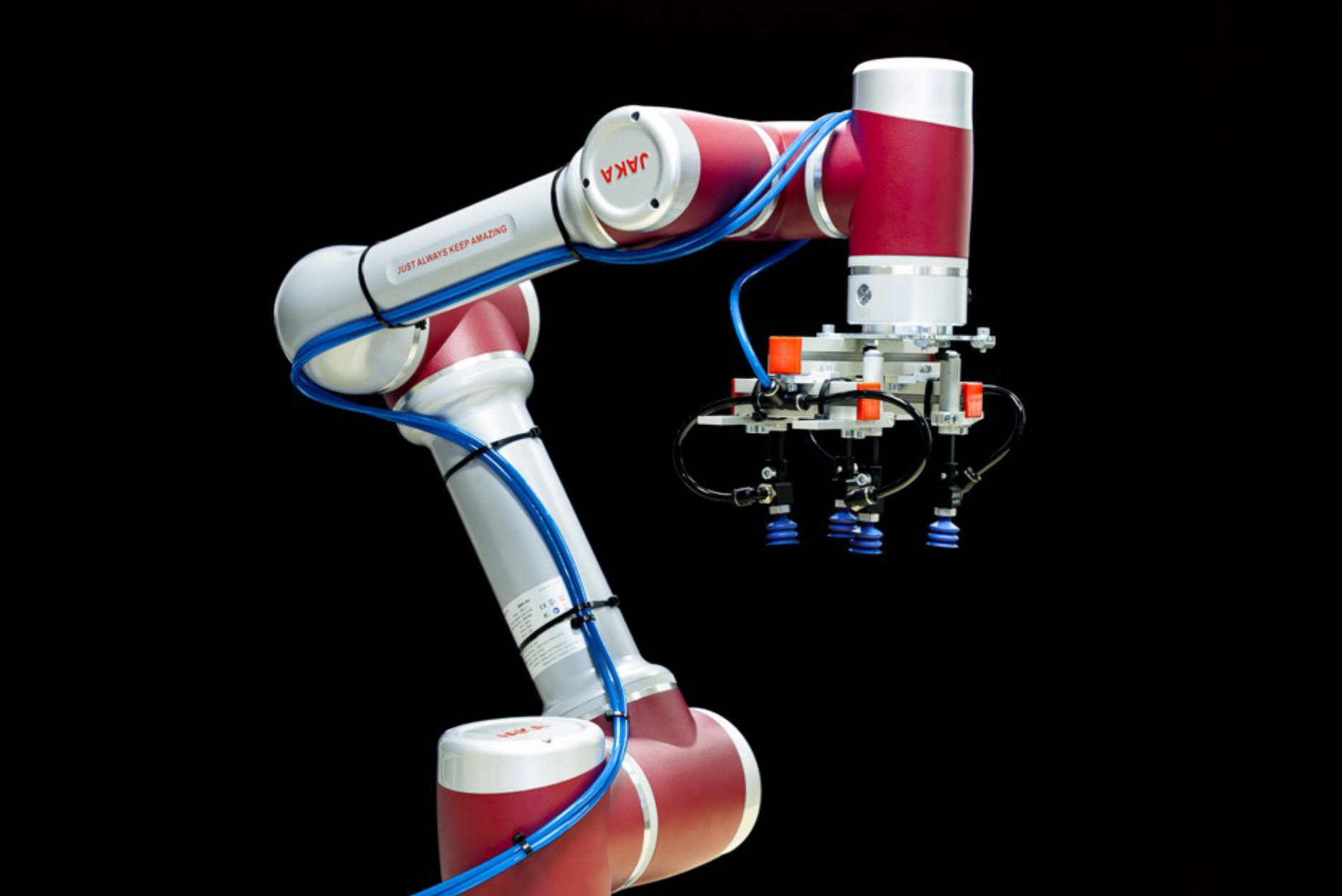
Running over a 24 hour shift pattern, we have the capacity to offer plastic injection moulding from small lot production to mass volume.
Our skilled process technicians have vast experience in a wide range of technical and engineering polymers.
Both within tool design and the moulding facility we have been at the forefront of metal replacement for the last two decades. During the developmental processes, we have confronted and solved many technical issues to ensure that the integrity and stability of a metal component are maintained with a plastic equivalent. We have vast knowledge and experience in overmoulding onto inserts and other plastic components.
Our toolroom is within the factory, to back up and maintain consistent production and tool maintenance. We mould tools manufactured by ourselves and that have been provided to us by our customers. Having, seen an increase in reshoring of moulding services, we offer tool assessment and trials in order to make this transition as smooth as possible.
Andel’s injection moulding customers, cross a wide range of industry sectors., increasingly we have been approached to supply added value services to ensure manufacture of parts within one factory. During the last decade we have invested in a Class 7 Cleanroom for medical device assembly and packaging. Additionally we offer Ultrasonic welding services and Heat Staking of inserts outside of the moulding process. More recently Pad printing has been added to our list of capabilities.