The quality of an injection moulded component relies upon both good design and accuracy of the injection mould tool. Andel Plastics has built a strong reputation for manufacturing precision engineered tooling cost effectively.
At Andel we like to build relationships with our customers, which means getting involved in a project from the concept stage. Customers have come to us with an initial idea, which can be as straightforward as a sketch or with full CAD models.
We find this approach, of being involved at the early stages of a project provides the best outcome all round. Ensuring that we understand the mechanical requirements and working environments of a component, means that our design feasibility is carried out with the injection mould tool design in mind. We are able to use our in-house mouldflow analysis system to advise on any potential issues with design before any steel is cut.
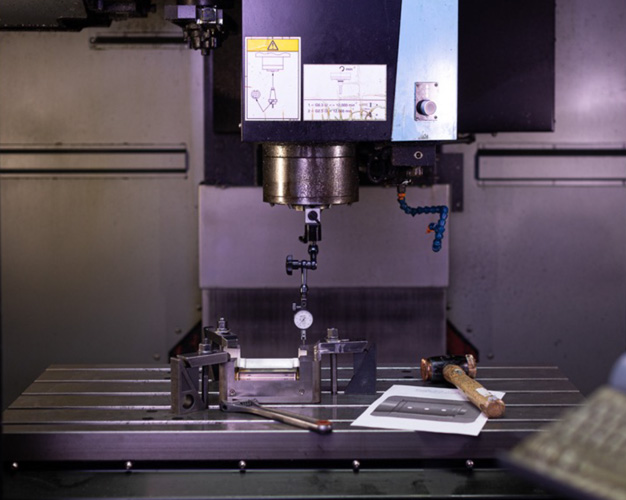
Over the last few years Andel Plastics has worked with Universities to research and develop 3D printed tooling in order to be able to provide rapid prototyping options to customers. A gamechanger in our industry.
We also offer a range of standard bolster sets, should the component be suitable, capital investment in tooling would be limited to the inserts and ejector plates. This solution provides reduced toolmaking leadtimes and costs. Should the project them ramp up we can supply the bolster to provide a full toolset, or manufacture multicavity tooling to suit requirements.
Being in the same factory as our moulding facility reduces downtime on production, modifications or maintenance.
That said we manufacture tooling for other moulders as well as mould tools that have been free issued by customers.
We are so confident in the quality of our production tooling, that we provide a ten year no maintenance guarantee for tools we design, manufacture and mould*
This excludes magnet tooling due to the aggressive nature of the polymer. Wear parts that have been highlighted during the dfm will be excluded –
- Design for manufacture
- Mouldflow analysis
- Modifications and repairs
- Prototype tooling
- 3D printed tooling
- Production and multi cavity tooling
- Insert and overmould tooling